Brewery Construction Process and Procedure
In recent day, some of customer are confused how to build the brewery, and what’s the brewery building process and procedure, now let’s we tell you how to build it. Part 1: What we will do for brewery building?
1.1Project Perfomance Processing
1.2Confirm the brewing request
Firstly, we will confirm more details about your brewery, such as beer type, brewery batchese per day or time, beer plato, fermentation period, brewery height, and etc.
Next We will proposal you according to your confirmation and details. We will sign a contract after both agree the coorperation terms and re-confirm the proposal, price, layout, brewing process before terms.
1.3 Preparation works before production
Re-check all proposal, layout, flowchart and re-confirm the details of brewery equipment.
And the tank drawing and 3D brewery model will be made and let you confirm, you will see what your brewing looks like.

1.4 Ramaterial preparing
Ramaterial booking: we will book the raw mataterial and dish head first according to confirmed tank’s drawing, and other accessories will booking, like motor, pump, chillers, as these items need UL Certificated, which takes longer time.
When the material has reached our factory and ready to production, we will send you our material sheet, and you will see the material’s ingredient, thickness, standard and etc.
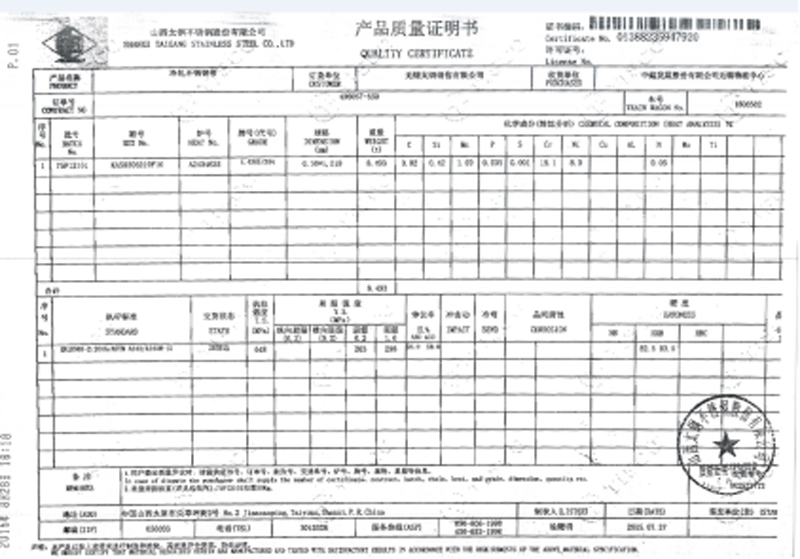
(SS plate quality certification for reference.)
1.5 Start to production
-Material cutting: Laser cutting, accurate cutting, flat edge without burrs.
-Sheet metal: Treatment of the plates and other processes in accordance with production.
-Assembly: Welding the cone and cylinder together, dimple cooling jacket, legs and other.
Welding adopt TIG welding way, which has better air tightness and can reduce the porosity of the weld during the welding of the pressure vessel.
-Polishing: Internal surface will treated with machinary polishing, and welding line polished to a belt for a better view. After that, the tank internal will treatment with packling pasivition, Internal surface roughness is 0.4um.
-Pressure testing: After completed, the cylinder and the jacket are hydraulically tested. The test pressure of the inner tank is 0.2-0.25mpa, and the test pressure of the dimple jacket is 0.2MPa.
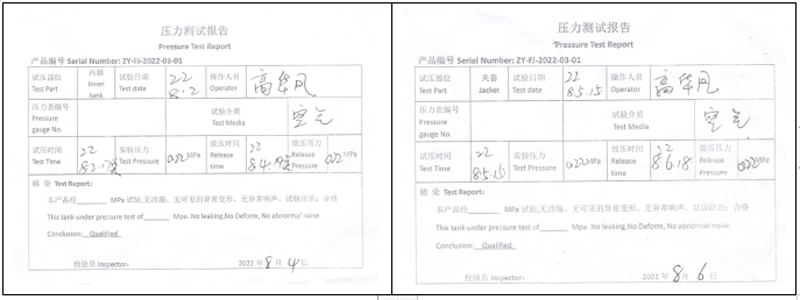
-Production inspecting: It will be checked after completed each process, and there is Process circulation card for next process. Afte completed the tanks, our inspector will check the details finally and inform our assembly workshop to move for the next step.
-Pipeline Assembly: Brewhouse pipelines will connect according to brewing flowchart and we will consider the pipeline if conveniet when brewing, and glycol pipeline pre-assembled as well according to layout.
-Debugging: we will connect the water and electric to make the brewery running in our factory.
Here it’s debugging video we did before to testing our system. Pls check it: https://www.youtube.com/watch?v=wCud-bPueu0
-Package: After finished the debugging, we will stick the labels on each connection and pipes for easy installation in site. And will pacakged it with Bubble film and anti-collision cloth, etc.
All valves and fittings will be wrapped with plastic wrap and the tank will be packaged or supported according to equipment dimension and container size.
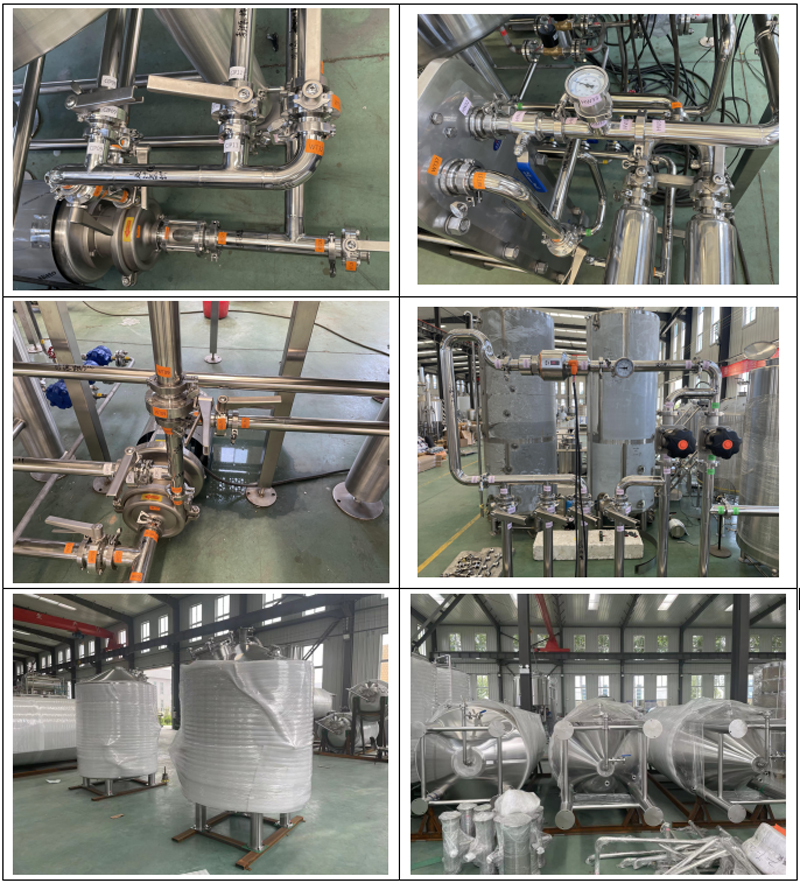
-Loading and delivery: The equipment will be loaded after we confirmed the shipping date and loading. All package will be detailed mark what's the accessories inside and send our client after delivery.
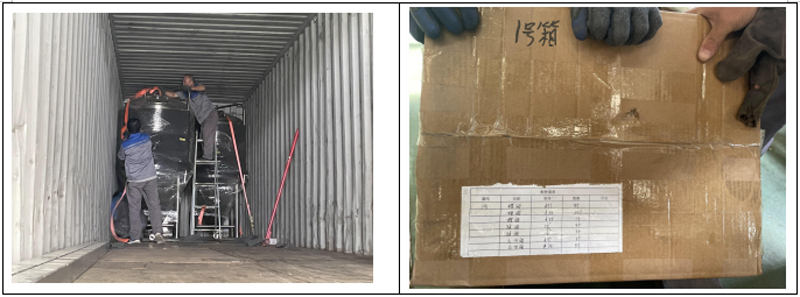
Part 2: What we will do for brewery designing?
2.1 Brewhouse: Highly matched with your brewing request.
Brewhouse part is the most important part in whole brewery, which is directly related with the wort and beer quality. Brewhouse design must follow exactly your brewing recipe, eg the average beer gravity/plato.
Make sure the Mash or lautering process can be finished in reasonable time.
Lauter tank: For Example 1000L brewery, The diameter of lauter tank is 1400mm, when the wort is 13.5 degrees, the malt feeding amount is 220KG, the equipment using efficiency is for 75%, and the thickness of the grain layer is 290mm;
When the wort is 16 plato, the feeding amount is 260KG, the tank volume using for 80%, and grain bed thickness is 340mm.
That's to ensure the thickness of the filter layer meets the brewing requirements, does not affect the filtration speed and ensures the production efficiency. Final to improves the output per unit time through reduces the filtration time.
Boiling kettle: The kettle volume design is based on the 1360L wort befor boiling, and the using volume is 65%. Because of the wort concetration is relative higher in America, the form will much abundant when boiling.
In order to prevent foam overflowing from the kettle during the boiling process, we use the forced circulation function to improve the evaporation rate to ensure the evaporation rate is 8-10% and improve the boiling intensity.
A forced circulation with kettle helps increase the evaporation, and the DMS situation and the content within 30PPM, it will reducing the heat loading and ensuring the stability of the wort chroma and avoiding the wort Maillard reaction.
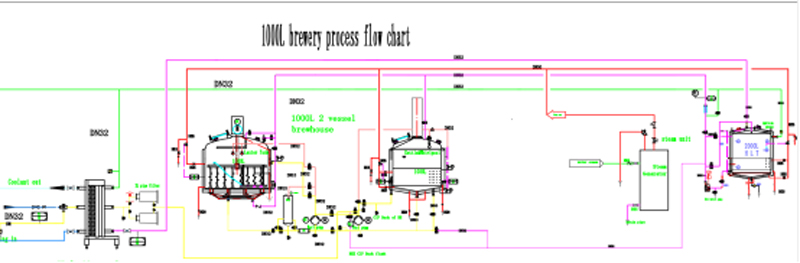
2.2 Lower energy consumption in brewery
Condensor system: The boiling kettle adopt steam condensation recovery system, it will helps to improve the water recovery and save the water and electric consumption in whole brewery.
The recovery hot water temperature around 85℃, and hot water recovery capacity at 150L for each batch; That's means it will save the electic 18kw per batch of the water temperature from 25-85℃.
Wort cooler: The wort heat exchanger area calculate by the brewing process and finish the cooling process in 30-40 minutes, and hot water temperature at 85℃ after heax exchange, heat exchange efficiency of more than 95%.
Therefor, we will ensure the maximum energy recovery and lower production costs.
2.3 Easy brewing and reducing maintaining in brewing process
A double strainer configured, in case the client brewing too hoppy beer. So we bring good guarantee on plate heat exchanger, which is the hardest part for cleaning.
The dual pump is necessary for glycol unit, for good guarantee when there is any maintaining request, each pump can be switch easily for keeping the production ongoing.
Dual chiller configured, with the same purpose like glycol pump.
Glycol pump used constant pressure pump and keep the same pressure in whole glycol pipelines, protect the soleniod valve and expanding the using life.
All these details is for the more stable work in whole brewery ruuning, and bring you a good experience in the brewing process.
Part 3: What's the preparation time required?
Now in order to clear the order process, we made a timeline of brewery system, pls see that.
Hope we can help you to build a perfect brewery in your planning.
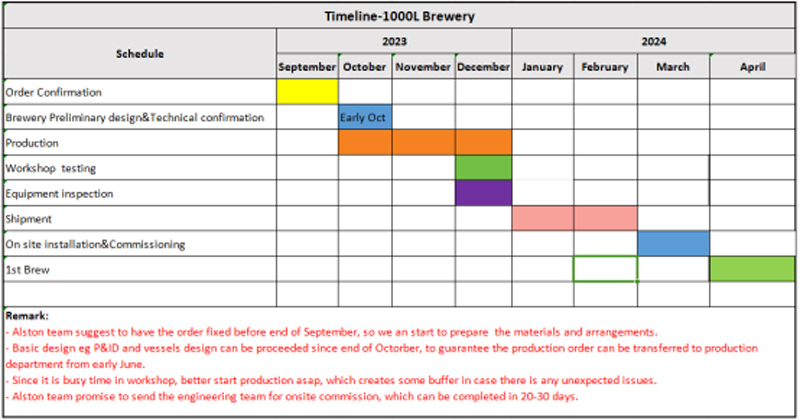
At the end, we are looling forward to work with you soon. Through this cooperation, you will feel our service and value.
Not only we should build a perfect brewery for you, also we are more focus on to establish a long -term cooperative relationship to achieve a win-win situation between our two sides.
Thanks for your time.
Cheer!